During their celebrations for hitting a milestone deployment of 1000 autonomous trucks, EACON Mining Technology unveiled the latest evolution of their SurfaceSupervisor system, an intelligent solution to be mounted on light vehicles. This system enables fast, accurate mapping of site conditions including windrow heights, back slope and cross slope gradients, ramp gradient, and curve radius. SurfaceSupervisor also detects surface hazards such as spillage, ruts, potholes, and other open-pit mining risks. Alongside the mapping capabilities, real-time calculations and data visualisation provide operators with a complete, in-depth view of sites and obstacles. This latest upgrade underscores EACON’s dedication to innovation, product excellence, and driving greater efficiency across the mining industry.
Transforming Mine Inspections with Automation
In the quality management of open-pit mine projects, many sites still rely heavily on manual processes for tasks to assess critical factors such as windrow height, slopes, road flatness, and gradients. While some advanced technologies exist, their implementation is often limited due to high costs, integration challenges, and operational constraints. As a result, operators are frequently exposed to hazardous conditions, extreme heat, and difficult terrain to collect essential data – leading to safety risks, inconsistent reporting, and potential operational delays that drive up maintenance costs.
EACON’s SurfaceSupervisor revolutionises quality control through real-time measurement and dynamic result visualisation – improving accuracy, traceability, and on-site responsiveness.
Combining AI-Driven Algorithms with High-Performance Hardware
The SurfaceSupervisor system integrates AI-driven algorithms with a robust, high-performance hardware suite, comprising a LiDAR, perception camera, and high-precision navigator. This hardware is fully in-house engineered for seamless integration and interoperability across a wide range of vehicle models. The fusion of LiDAR and visual perception technology enables real-time data acquisition, high-resolution modelling, and precise obstacle recognition, ensuring superior measurement accuracy.
To streamline operations, SurfaceSupervisor utilises ORCASTRA® CREW, an intuitive control panel with an optimised human-machine interface for effortless survey management. ORCASTRA® CREW is capable of working both independently and in tandem with ORCASTRA® CONDUCTOR, the autonomy and production management system, which provides real-time digital oversight of mine site quality. Together, these systems form a closed-loop ecosystem, seamlessly interacting with autonomous haulage trucks and roadside units to improve operational intelligence.
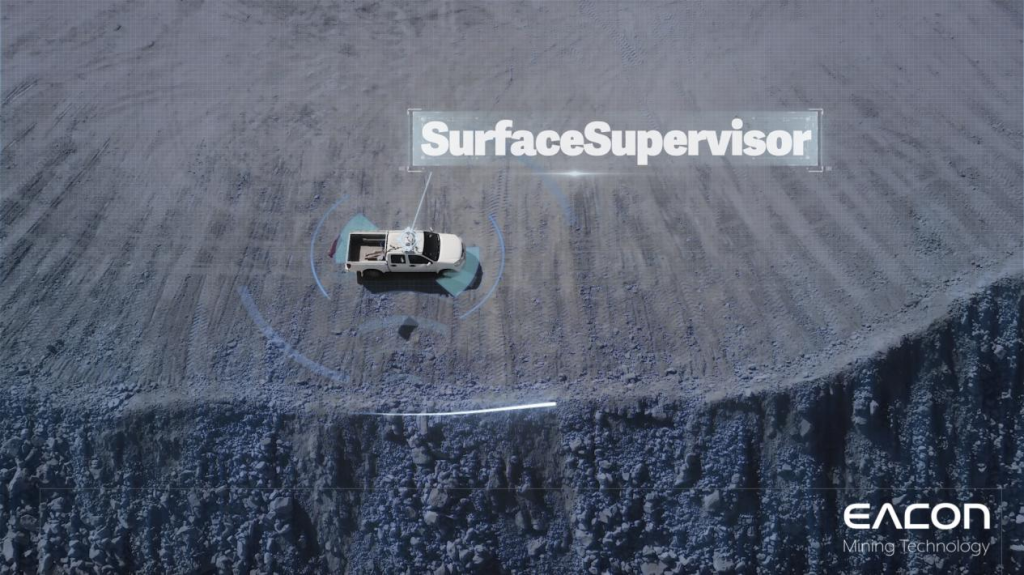
SurfaceSupervisor Monitoring for Hazards
Optimising the Future of the Mining Industry
To date, the SurfaceSupervisor system has been successfully deployed in nearly 20 open-pit mines. Looking ahead, next-generation mine inspection solutions are expected to realise automation of the entire process, delivering a future of “zero contact, zero delay, zero errors, and zero accidents”. As a leader in mining innovation, EACON remains committed to driving this transformation and creating significant value for mine operators.
About EACON
EACON Mining, founded in 2018, focuses on providing turnkey autonomous haulage solutions designed to optimise surface mining operations. Our autonomous haulage system, ORCASTRA®, is fully interoperable with OEM equipment and features a distributed architecture underpinning ultimate adaptability for optimum performance in even the most demanding open-pit mining environments. Coupled with EACON’s expertise in emission-reducing powertrain solutions, we offer hybrid-electric, battery-electric, and retrofitted autonomy across off-highway OEMs — driving a safer, greener future for the mining industry.
For more information on EACON’s intelligent surface solutions, visit eacon.com/en.
Contact:
Evelyn Zhu, Communication Manager overseas@eacon.com